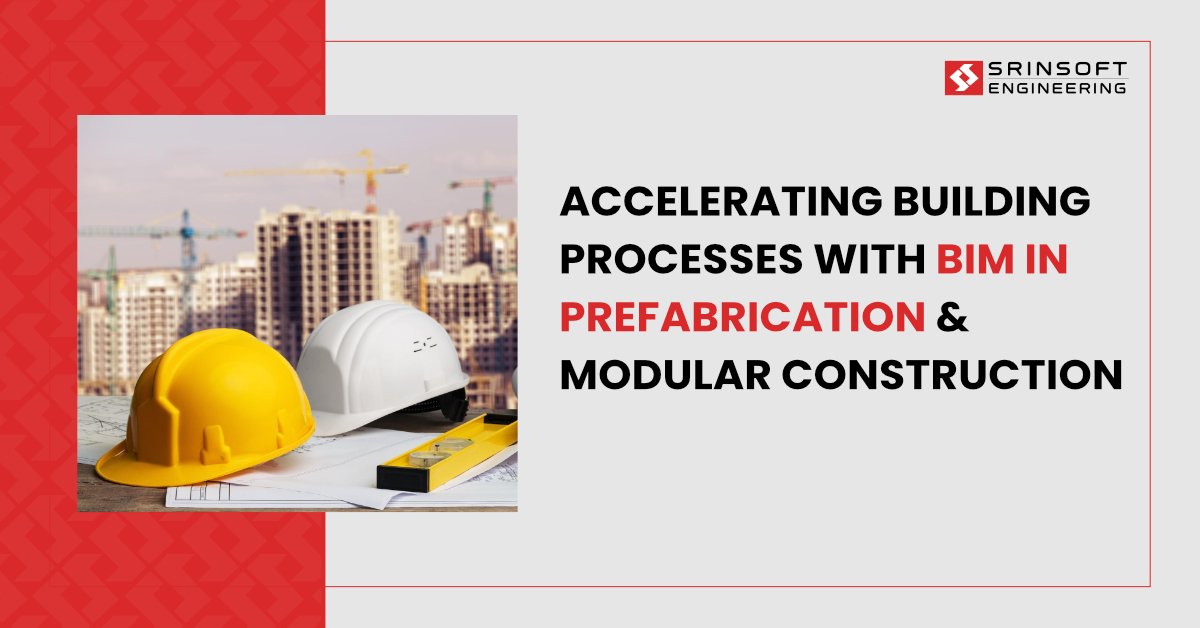
Prefabrication and modular construction methods have gained significant traction in the construction industry due to their ability to accelerate building processes, improve efficiency, and enhance project outcomes. testings
Building Information Modeling (BIM) plays a vital role in facilitating and optimizing prefabrication and modular construction.
In this article, we will explore how BIM enhances prefabrication and modular construction, leading to faster project timelines, improved quality, and increased productivity.
Detailed 3D Modeling
BIM enables detailed 3D modeling of prefabricated components and modular elements.
With BIM, designers can create precise virtual representations of prefabricated modules, considering their exact dimensions, connections, and integration with other building systems.
This level of detail allows for accurate visualization, clash detection, and coordination before the manufacturing and assembly processes begin.
Streamlined Design-to-Fabrication Workflow
BIM streamlines the design-to-fabrication workflow by seamlessly connecting the design phase with the fabrication and assembly stages.
Design information from the BIM model can be directly used by fabricators and manufacturers to generate shop drawings, fabrication details, and production schedules.
This integration eliminates the need for manual rework and reduces errors, ensuring smooth transitions and efficient processes.
Improved Collaboration
BIM promotes collaboration among project stakeholders involved in prefabrication and modular construction.
Designers, architects, engineers, fabricators, and contractors can work together in a shared BIM environment, allowing for real-time collaboration and information exchange.
This collaborative approach ensures that all parties are aligned, resulting in improved design coordination, reduced conflicts, and enhanced project outcomes.
Clash Detection and Conflict Resolution
The clash detection capability of BIM is particularly valuable in prefabrication and modular construction.
BIM software can identify clashes between prefabricated components, building systems, and existing structures before manufacturing and assembly.
This early clash detection enables prompt resolution, minimizing costly rework during on-site installation and ensuring smooth assembly processes.
Accurate Material Quantification
BIM provides accurate material quantification for prefabricated components and modular elements.
By extracting data directly from the BIM model, project teams can generate precise quantity take-offs, facilitating procurement and reducing material waste.
Accurate material quantification leads to optimized supply chain management, cost savings, and improved project efficiency.
Off-Site Construction Planning
BIM supports off-site construction planning by enabling visualization, sequencing, and coordination of prefabricated components and modular elements.
The 3D model allows project teams to plan assembly sequences, transportation logistics, and on-site installation processes in a virtual environment.
This proactive approach enhances construction efficiency, minimizes on-site disruptions, and improves overall project schedules.
Enhanced Quality Control
BIM facilitates enhanced quality control in prefabrication and modular construction.
Through the use of BIM, project teams can conduct virtual inspections, perform simulations, and validate the design before fabrication.
This reduces the likelihood of errors and ensures that prefabricated components meet the required specifications, resulting in higher-quality construction and improved building performance.
Conclusion
By leveraging the power of BIM in prefabrication and modular construction, projects can achieve accelerated building processes, improved efficiency, and enhanced project outcomes.
The detailed 3D modeling, streamlined workflows, improved collaboration, clash detection, accurate material quantification, off-site construction planning, and enhanced quality control offered by BIM contribute to the success of prefabricated and modular construction projects.