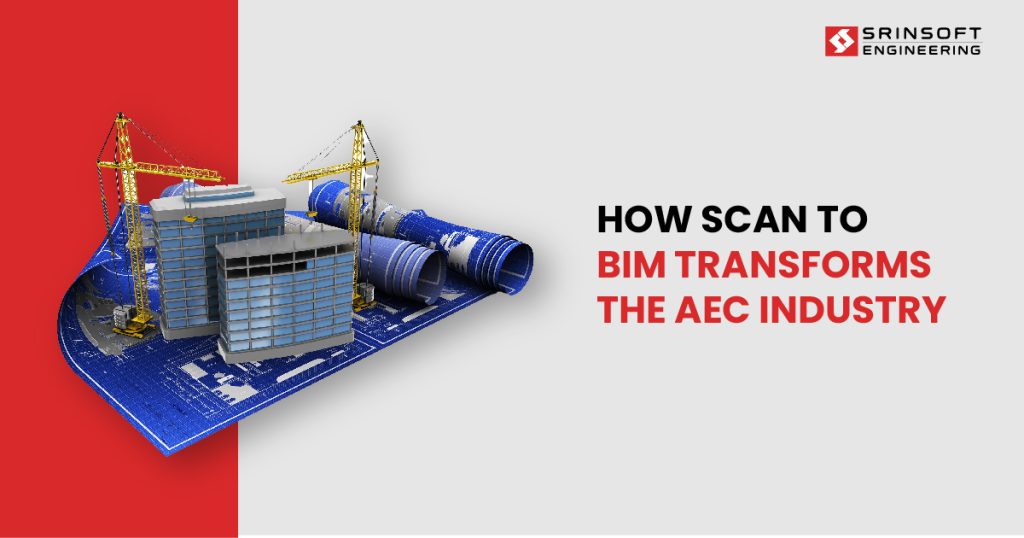
The Architecture, Engineering, and Construction (AEC) industry is continually evolving, embracing innovations and techniques to enhance the construction field.
Scan to BIM is a fantastic tool that brings order to the hectic AEC landscape, effectively tackling the industry’s fragmented workflows while meeting the rising demand for digital solutions.
This remarkable technology integrates spatial data from laser scans, point clouds, and existing building information into a single, unified 3D digital model, capturing not just the physical asset, but also its interconnections.
What is Scan to BIM?
In a Scan to BIM process, a laser scanner is used to capture an accurate 3D scan of the real-world conditions on a project. The scan data is then imported into a 3D modeling environment to create either accurate as-built models or to inform the design with the real-world conditions.
How Scan to BIM Works
Scan to BIM is the procedure that transforms the data from laser scanning into a digital 3D model. Here is the step-by-step procedure of the process:
1. Identification of Information Requirements:
Determine the necessary details for the model, which can be the required level of detail, specific building elements, and so on.
2. Scan Planning:
Define parameters for scanning, including accuracy, resolution, and coverage. This is what ensures scanning captures all necessary data
3. Scanning:
Scan a physical space by using a 3D laser scanner. Millions of data points are collected by the scanner that compiles into forming a point cloud representing the site geometry
4. 3D Modeling:
Transform point cloud data into a 3D BIM model. The model can be used for various purposes, including design, construction, and facility management
This process enables the creation of accurate and detailed digital representations of physical spaces, which can be invaluable for new construction projects, renovations, and more.
Problems That Scan-to-BIM Can Solve
Scan-to-BIM (Building Information Modeling) is a technology that leverages laser scanning or other 3D scanning techniques to capture accurate as-built data of a physical structure and convert it into a digital model. This method solves a variety of problems, including:
1. Accuracy Challenges in As-Built Documentation
❓ Problem:
Traditional methods of documenting existing buildings often lead to inaccuracies, missed details, or costly mistakes when creating renovation or retrofitting plans.
✅ Solution:
Scan-to-BIM provides precise, high-resolution data, ensuring accurate as-built documentation of all physical features, down to minute details. This reduces errors in the design and construction phases.
2. Difficulties in Managing Costs and Time
❓ Problem:
Manual measurement and survey methods are time-consuming, prone to human error, and can be disruptive to ongoing operations.
✅ Solution:
3D laser scanning automates data collection, drastically reducing the time needed to capture site conditions. It’s also non-intrusive, making it suitable for buildings in use.
3. Handling the Complexity of Existing Structures
❓ Problem:
Renovating or repurposing an old or complex building often presents challenges due to limited or outdated drawings.
✅ Solution:
Scan-to-BIM provides a detailed and accurate 3D model, helping architects, engineers, and contractors understand the existing conditions, thus simplifying the design process and minimizing unforeseen challenges.
4. Coordination and Collaboration Gaps in BIM Workflows
❓ Problem:
Coordinating between different teams or disciplines (architects, engineers, contractors) can lead to discrepancies and rework.
✅ Solution:
The scan-to-BIM model serves as a shared platform where all parties work from the same up-to-date digital model, improving collaboration and reducing conflicts between disciplines.
5. Inefficiencies in Clash Detection and Risk Mitigation
❓ Problem:
In complex construction or renovation projects, design and construction errors like clashes between systems (e.g., HVAC, electrical, plumbing) can lead to costly delays.
✅ Solution:
With scan-to-BIM, potential clashes or issues are identified during the design phase using 3D visualization, reducing the risk of issues emerging on-site and preventing costly changes during construction.
Steps of Scan to BIM Process
- Define the goal of the data collection to ensure efficient scan data capture.
- Send a team member to the project site for scanning.
- The scanner operator sets up the equipment, adjusting parameters like scan density.
- Capture multiple scans from different locations to ensure full coverage (limited by line of sight).
- Transfer scan data to a computer via USB or cloud platforms like Trimble Connect.
- Register individual scans into a composite point cloud using modelling software.
- Import the point cloud into modelling software to create constructible content.
Applications of Scan to BIM across Building Phases
1. Point Cloud Data
- Definition: A point cloud is a collection of data points in space, representing the structure’s geometry in 3D space.
- Use: It provides an accurate and highly detailed digital representation of the scanned environment, including both major and minor architectural elements. Point clouds can also capture variations in surface texture and shape.
- Format: Typically, in formats like .xyz, .pts, or .las, which store the coordinates of each point.
2. BIM Modelling
- Software Integration and conversion: Point cloud data is imported into BIM software like Revit. The point cloud data creates 3D model using the real time software. The model contains both MEP and Architecture feathers.
- Output: The output is a digital twin which is a virtual representation of the physical structure which is useful in many tasks.
3. Design & Analysis
- Renovations & Space Planning: With the BIM model, teams can plan renovations, analyze spatial usage, and simulate different design scenarios before any construction begins.
- Simulation: BIM tools indicate the simulation process to check the design.
- Clash Detection: to detect any potential clashes between building systems (e.g., pipes running through walls or electrical systems interfering with HVAC installations).
- Collaboration: BIM software allows various collaborations between stakeholders like architects, engineers and contracts with shared model space.
Key Benefits of Scan to BIM
- Authenticity: 3D laser scanning provides extremely precise data, reducing errors and omissions in the modelling process.
- Efficiency: Using BIM to convert point cloud data into a 3D model saves time, particularly for complex or existing structures.
- Collaboration: BIM supports interdisciplinary collaboration, ensuring that all parties work off the same accurate model.
- Lifecycle Management: The digital twin created can be used for facility management, monitoring, and future renovations.
Challenges and Limitations of Scan to BIM
1. High Initial Costs
Challenge:
The necessary equipment for 3D scanning, such as LiDAR scanners, along with specialized software for processing point cloud data, represents a significant financial investment. Furthermore, qualified personnel are essential for the effective operation of these tools.
Limitation:
Smaller organizations may struggle to justify the initial capital outlay, particularly if their project volume requiring scanning is limited.
2. Data Complexity and Size
Challenge:
Scan-to-BIM processes yield extensive amounts of data, particularly in the case of large or intricate buildings. The point cloud data can be exceptionally detailed, resulting in substantial file sizes that can be challenging to manage and process efficiently.
Limitation:
Handling these sizable datasets can be labor-intensive and may necessitate high-performance hardware, posing a potential hurdle for teams lacking access to robust computing resources.
3. Data Processing and Conversion
Challenge:
Transforming raw point cloud data into a fully functional BIM model takes a bit of specialized know-how and the right tools. This process isn’t always smooth sailing; it often requires some manual tweaks to tidy up the data.
Limitation:
If the point cloud data has inaccuracies—like occlusions or scanning errors—it can lead to quite a bit of extra work to ensure that the final model is reliable and ready for use.
4. Scan Accuracy and Quality
Challenge:
The precision of a 3D scan can be impacted by various environmental factors, such as lighting, surface reflectivity, and any objects blocking the scanner’s view.
Limitation:
Sometimes, the scan might miss capturing finer details or certain areas, which can create gaps in the data or necessitate additional scanning.
5. Integration with Existing Systems
Challenge:
Merging Scan-to-BIM data with other systems like Project Management Software, Energy Modeling Tools, or Facility Management Systems can be quite intricate.
Limitation:
Compatibility hiccups between different software can slow down workflows and may require further investment in custom integrations or middleware solutions.
6. Learning Curve and Training
Challenge:
The technology and software utilized in Scan-to-BIM can be quite complex, necessitating a good amount of training and expertise.
Limitation:
Team members need to be trained to handle scanning devices, manage data processing, and create accurate BIM models, which can take time, especially in environments with high staff turnover.
7. Handling Dynamic Changes
Challenge:
In projects where changes happen frequently, keeping the Scan-to-BIM model up-to-date in real-time can be quite the task.
Limitation:
Maintaining consistency between scanned data and the ongoing construction or renovation involves continual scanning, and frequent updates can add to costs.
The Future of Scan to BIM in the AEC Industry
Following is a summary of the features and trends and impact of the scan-to-BIM implementation in AEC.
1. Increased AI Automation
The AI will aid in the automation of the conversion from scans to precise BIM models, in turn resulting in efficiency gains, a reduction of errors and the freeing of the designer’s time to be used for design and problem solving.
2. Cohesive Integration of Digital Tools
Scan-to-BIM will be seamlessly combined with AR, VR, IoT and GIS to promote visualization, collaboration, real-time decision-making, AR site visits and data-driven modeling.
3. Mobile Real-time and Mobile RT-Scanning
Data-based acquisition data obtained by LiDAR and drone will enable mobile real-time acquisition, the data will be continually updated within the model and the risk of erroneous construction errors will be significantly mitigated.
4. Collaboration Through Cloud
Cloud platforms will enable simultaneous collaboration and real-time updates to the model which will enhance communication and flexibility for project teams working in different locations.
5. 5D BIM with Cost Estimation
Scan-to-BIM will combine with 5D BIM to automatically generate accurate cost, and timeline estimates from the actual scans received, optimizing the project.
6. Facility and Lifecycle Management
Scan-to-BIM will be essential for facility management, as data from IoT sensors and maintenance activities will be used in real time to track building performance and schedule remodeling activities.
Srinsoft Engineering for Expert Scan-to-BIM Solutions
Srinsoft Engineering is known for its precise Scan-to-BIM services customized to the growing needs of the AEC industry. We master the 3D laser scanning, point cloud conversion, and BIM modeling process to bring out accurate, data-driven renovation solutions, facility management, and clash detection solutions. With commitment to the use of the latest technology and easy collaboration, we assist architects, engineers, and contractors in streamlining their workflow, minimizing the risk associated with a project, and improving productivity. Partner with us today to transform your projects with precision and innovation. Contact Srinsoft Engineering to learn more!
Conclusion
The influence of the right BIM modeling services to your project will run from conceptualization all the way to construction and beyond. When you understand the needs of your project, then evaluate the experience of the provider in good fit toward collaboration, flexibility, and cost, you maximize value and ensure the best outcome for your project.