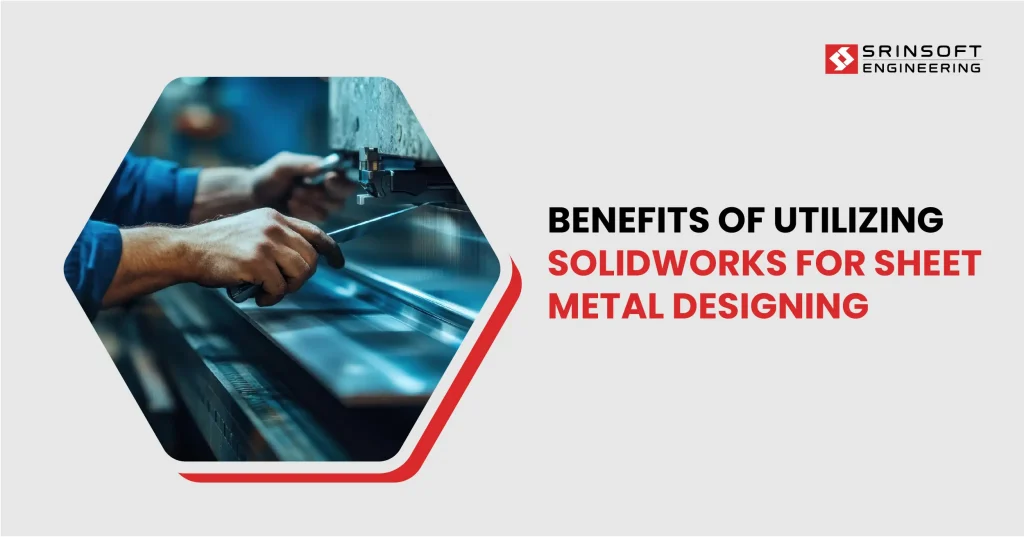
Sheet metal design involves conceptualizing, creating designs for products and components made from thin, flat metal sheets.
These designs are crafted with careful consideration of the manufacturing process, tooling, and materials to ensure optimal functionality, durability, and cost-effectiveness.
Sheet metal design demand varies by country, influenced by industrialization, infrastructure development, and manufacturing capabilities. It is widely utilized in industries like automotive, aerospace, electronics, and construction.
SOLIDWORKS 3D CAD is a top-tier parametric design software used in various industries for rapid product development and design innovation, including industrial equipment, medical devices, high-tech home and lifestyle
Challenges for Sheet Metal Fabricators
Creating great designs and drawings calls for multiple skills, knowledge bank of manufacturing processes and materials, need for cost consciousness, and a brief of manufacturing capabilities.
Thus, a sheet metal designer wears multiple hats to deliver optimized, manufactured, and robust designs consistent with fabrication methods and operational conditions.
Some of the challenges that SME sector manufacturers face is:
- Creating error-free models with sheet metal features and DFM guidelines.
- CAM integration with PLM or cloud technology in CAD for cost-effective solutions.
- Capturing DFM needs and freeform development with complex CAD software architecture.
SolidWorks offers a good fit for end-to-end drafting needs, from concept development to detailed technical drafting. It has a set of tools dedicated to sheet metal design drafting that can help create parts with ease.
How SolidWorks Transforms Sheet Metal Design and Drafting?
SolidWorks revolutionizes sheet metal design and drafting by offering powerful, specialized tools that simplify and streamline the entire process.
From concept development to final detailed drawings, SolidWorks enables designers to create accurate, error-free models that follow Design for Manufacturing (DFM) guidelines.
With its intuitive interface and dedicated features, SolidWorks helps fabricators optimize designs for manufacturability, reduce production costs, and improve overall efficiency, making it an essential tool for modern sheet metal design and drafting.
1. Conceptualization
The design process for sheet metal components involves conceptualizing the components based on functional requirements, constraints, and aesthetics.
As a 3D CAD modeler, understanding manufacturing optimization allows for accurate and positive outcomes.
SolidWorks automatically assigns a metal component as a sheet metal part, providing specialized instructions for product design.
2. Create Parts With Constant Sheet Thickness and K-Factor
Sheet metal parts are typically fabricated from metal sheets with appropriate thickness. The spring back factor or “K” factor is necessary for perfect bends and unrolled/flattened sizes.
SolidWorks sheet metal modeling allows users to choose material, thickness, and K factor, and add user-defined properties.
3. Leverage SolidWorks Flexibility for Complex Sheet Metal Shapes
The CAD designer or the engineer might not have the opportunity to start with the sheet metal module every time.
In this scenario, one can start with the free-form concepts of 3D solid models or surface creation and these models can then be converted into sheet metal using convert to sheet metal option with relevant thickness.
Read More: What Is Structural Steel Detailing
4. Design Optimization
Design optimization services improve sheet metal components’ performance, efficiency, and cost-effectiveness through iterative analysis, simulation, and refinement using advanced tools for material reduction, weight reduction, structural integrity optimization, and manufacturing process streamlining.
5. Begin by Considering the Center and Symmetry
Symmetry in 3D modeling can significantly save manufacturing time by enabling quick adjustments like setting up cutter home positions, positioning raw sheets, and optimizing nesting.
Techniques like mirroring and mating can also be used effectively. This approach offers flexibility and freedom from the start of the design process, preventing rework.
The user experience is tailored for sheet metal designers, streamlining the design process and eliminating the need to learn a comprehensive CAD system.
Typical challenges are easily solved through easily accessible tools, reducing user interface clutter.
6. Flexibility and Features
SolidWorks offers the flexibility to design the part as a non-sheet metal 3D model to convert it into sheet metal to incorporate DFM requirements.
SolidWorks 3D intuitive design for sheet metal gives you the design flexibility to produce sheet metal parts and accurate virtual prototypes. Ideally, a single 3D model for sheet metal products should have comprehensive design features to ensure clear design intent communication.
SolidWorks is a tool that offers inbuilt tabs and slots for quick use, various types of flanges for creative design, and the ability to generate basic and advanced bends.
It also allows users to read bend tables for allowance and K factors, and create forming features like extruded flanges, embosses, louvers, lances, and ribs.
9 Benefits of SolidWorks for sheet metal designing
SolidWorks goes beyond basic design by offering advanced applications that fit perfectly into the digital product lifecycle and modern manufacturing processes. This means companies can take their product from the initial concept, all the way to prototype and manufacturing, much faster.
✅ SolidWorks offers robust parametric modeling capabilities that allow designers to create complex and highly customizable sheet metal designs with unparalleled efficiency and precision.
✅ It comes equipped with a comprehensive set of sheet metal features that are specifically designed to streamline the modeling of sheet metal components.
✅ SolidWorks offers advanced rendering and visualization tools with which designers can create realistic 3D models of sheet metal components.
✅ SolidWorks comes with built-in finite element analysis (FEA) capabilities. It allows designers to simulate and analyze the structural performance of sheet metal components in a virtual 3D environment.
✅ SolidWorks integration with manufacturing processes ensures a seamless transition from design to fabrication, generating accurate flat patterns, CNC toolpaths, and manufacturing drawings, minimizing errors, and streamlining production workflows.
✅ SolidWorks sheet metal modeling software offers powerful design automation tools that enable designers to automate repetitive tasks and streamline workflows.
✅ Customization of the software provides a user-friendly experience to the next level.
✅ SolidWorks offers a global variable equation to control the entire model by parameters and derived equations
✅ We can import or export MS Excel in SolidWorks to interlink the design table.
The SolidWorks 3D CAD tool helps metal fabricators to be more competitive and efficient. SolidWorks parametric modeling offers a new level of efficiency for fabricators, designers, and modelers. Dedicated SolidWorks modules can save time and costs, making sheet metal designing more organized and productive.
With design automation, repetitive tasks are reduced, allowing designers to focus on innovation. It streamlines everything, so you can make quicker decisions and get products to market faster.
If you’re new to the industry, think of SolidWorks as a powerful tool that not only helps create designs but also speeds up the whole process from idea to final product.
Conclusion
So, what are you waiting for?
SolidWorks is trusted by designers and engineers everywhere to bring their ideas to life with precise 3D models. By hiring a SolidWorks expert from SrinSoft Engineering, you get the most out of this powerful tool.
From designing sheet metal parts, mechanical components, industrial equipment to tools, our team is ready to support you every step of the way. We work with a variety of industries, so no matter what your project involves, we’ve got you covered.
Plus, you don’t have to worry about buying expensive software or setting up any infrastructure—we handle all that for you.
If you’re ready to see your designs, come to life, reach out to us today.